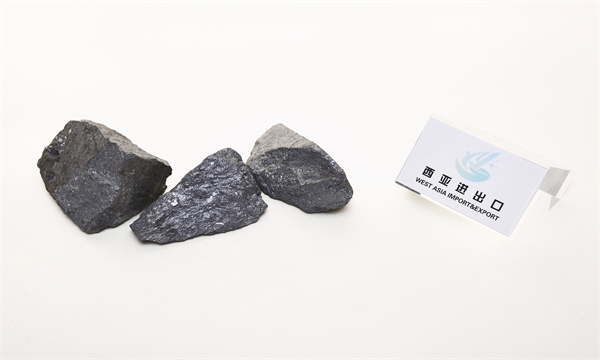
Silicon aluminum barium
Silica-aluminum-barium alloy has strong deoxidation and desulphurization ability, which plays an important role in changing the distribution of inclusions in steel, refining grains, improving the machinability of steel and improving the quality of steel.
- Grade: Si-Al-Ba etc.
- Size: Lump/Grain/Powder
The effect of Si-Al-barium alloy is more significant than that of single alloy such as aluminum block and Fe-silicon, which improves the utilization rate of alloy, reduces the cost of steelmaking and has better economic benefits.
Silicon alloy is a very widely used material in our daily application process. It is also used as a deoxidizer and desulfurizer in the steelmaking process.
Among the prior art, the preparation method of Si, Al and barium ferric has been disclosed in the following literature, among which CN89109528 has disclosed the topic of "Si, Al and Barium Ferric alloy for steel deoxidation and its preparation Method", which is characterized by the selection of different raw materials and ratio of ingredients, and the ore reduction furnace and induction furnace are two times combined.
CN95100005, published the title of "Production Method of Compound deoxidizing agent Silica-aluminum-barium Iron", which is characterized by the use of silica-aluminum-barium ore and iron filings as the main raw materials in a single smelting furnace. Its raw material composition (weight) is silica 10-38% bauxite 20-45% barite 7-14% iron debris 0.6-1.4% coke powder 13-23% coal powder 12-20% smelting temperature is 1700℃ ~ 2000℃, smelting time is 2-4 hours.
CN95100552, published the title of "Hot Furnace One-step Production Method of silica-aluminum-barium ferroalloy compositedeoxidizing agent", which is characterized by bauxite (or bauxite or bauxite), silica (SiO↓[2]), barite (or barium carbonate), steel chips (or iron ore) and coke (carbon added to the ore furnace one-step smelting into silica-aluminum-barium ferroalloy; In fact, the contents of this case and CN95100005 are the same.
The above mentioned silica-aluminum-barium iron basically adopts two methods. One is the combination of mineralorimetric method and induction furnace method, but this method still requires the use of metal aluminum, which leads to the increase of cost. In addition, due to the use of secondary smelting, the energy consumption is high. Second, the one-step method, namely the mineralogic method, is used to directly produce Si, Al and barium iron. However, due to the large number of raw materials used, it is difficult to control the production process, which leads to the decline of economic indicators.
The commonly used production method is also the use of silica barium iron and aluminum; Ferrosilicon plus barium plus aluminum, they are all using the medium frequency furnace method, so the same need for center of gravity melting, the same defects exist.
The purpose of the invention is to provide a new process for producing ferrosilica-aluminum-barium which can overcome the shortcomings of the existing process.
The purpose of the invention can be realized by directly mixing two liquid alloys in a certain proportion to obtain ferrosilicon aluminum-barium silicon when producing ferrosilicon aluminum-barium silicon.
The following is a detailed description of the invention, through which the invention can be clearly understood.
Among the existing technologies, the production process of ferrosilica-aluminum and ferrosilica-barium by mineral-thermal method is mature. For example, CN90104541 has disclosed a "production process of ferrosilica-silicate alloy", in which raw materials such as silica, barite, lime, coke and iron chips are mixed and directly injected into the mineral-thermal furnace to produce by carbothermal method. It overcomes the disadvantages of high energy consumption, high cost and low recovery rate of Ba and Si in the existing two-step production process of barium ferrosilicon alloy. Specifically, it is composed of the following steps a, the silica, barite after grinding sieve, and rinse with running water; b. The lime, coke and iron filings are broken and screened; c. Mix the raw materials prepared by a and b evenly and add them into the ore furnace intermittently for smelting; d. Iron is produced regularly, ingot is cast, and then finished into storage.
CN91101423 disclosed a "thermal production of silicon aluminum iron process", the main process of bauxite, bauxite, silica, iron filings and bituminous coal, its weight percentage is 21∶21∶ 6.3 ∶ 6.3 ∶ 45.4, The production process of Si Al Fe (alloy) formula is as follows: → raw material processing → batching → furnace melting → revamping ingot mould → oven filling mould → cooling demoulding → laboratory analysis → storage → finishing → packaging.
The above-mentioned processes for the production of ferrosilica-aluminum-silica-barium and ferrosilica-aluminum-barium are very mature. Therefore, the researchers adopted the method of mixing the two products in a proportional liquid state at the time of oven to obtain ferrosilica-aluminum-barium alloy directly.
Specifically, the proportion of each component of the required Si-Al-barium ferroalloy is determined first, and then the commonly used Si-Al-ferric and Si-barium ferroalloy produced by the existing process is selected. After calculation, Si-Al-ferric and Si-barium ferroalloy are mixed in proportion in the liquid state to obtain the final Si-Al-barium ferroalloy that meets the requirements.
Specifically, the second embodiment is to first determine the required proportion of each component of Si-Al-barium ferroalloy, and then select whether the simple proportional mixing of Si-Al-Fe-barium ferroalloy and Si-Al-Fe-barium ferroalloy can be obtained in accordance with the requirements. If the proportion does not meet the requirements, adjust the proportion of Si-Al-Fe-barium components. Then the adjusted proportion of Si - Al - Fe and Si - barium Fe were mixed proportionally to get Si - Al - barium Fe alloy.
Specifically, the third embodiment is to first determine the required proportion of each component of Si-Al-barium ferroalloy, and then select whether the simple proportional mixing of Si-Al-Fe-barium ferroalloy and Si-Al-Fe-barium ferroalloy in the existing production process can get the final Si-Al-barium ferroalloy that meets the requirements. If the proportion does not meet the requirements, adjust the proportion of components in Si-barium ferroalloy. Then the adjusted proportion of Si - Al - Fe and Si - barium Fe were mixed proportionally to get Si - Al - barium Fe alloy.
The first advantage of the invention is that it adopts the process of producing Si-Al-Fe and Si-barium Fe by mineralorimetry with relatively mature existing technology. In this way, it overcomes the defect that Si-Al-barium Fe produced by the existing process is difficult to control due to the large number of components. The second is the use of liquid direct mixing, overcome the solidification after melting a lot of energy consumption defect; Third, the proportion of each component is simple to adjust.